Delishi/Goodsjack Servo hydraulic press for Fuel Cell Bipolar Plate Forming Die. Continue to ship high-precision bipolar plate servo molding machines!
As a leading hydraulic press manufacturer in all areas of forming technology, Delishi/Goodsjack supply hydraulic press for the mass production of metal bipolar plates for fuel cells. The knuckle-joint press based on the Triton series for the BPL 25 and BPL 50 variants has been specially adapted to the requirements for the manufacture of bipolar plates by forming, for example to minimize the deflection of the bed and slide. Thanks to the use of knuckle joint kinematics, a lower deflection of the machine is achieved. Since a knuckle joint is never moved in the extended position, there is no need for a soft oil cushion for hydraulic overload protection, which increases the rigidity of the hydraulic press machine.
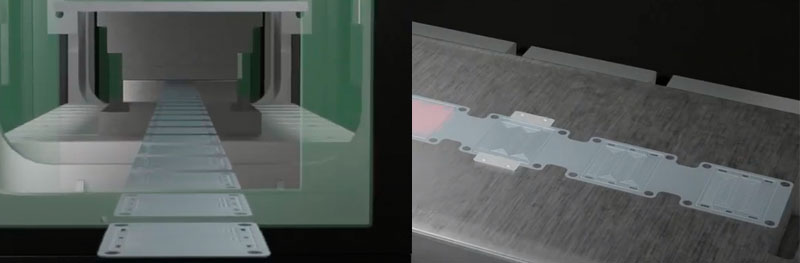
Process of Hydraulic Press for Fuel Cell Bipolar Plate Forming Die
The invention process for forming the bipolar plate of the fuel cell, which comprises the following steps: 1, blanking: a processed stripper is positioned between the steel mould and the accommodating frame; the template of the mould has relative motion under the action of a hydraulic machine and drives the steel mould to move; the steel mould and the accommodating frame carry out blanking and cutting on the processed stripper; and a billet obtained by the cutting enters the accommodating frame along the steel mould; and 2, stamping and forming: an upper mould enters the accommodating frame, continuously moves under the action of the hydraulic machine and extrudes the billet and rubber to allow the billet to be filled in a mold cavity of the steel mould so as to obtain the metal bipolar plate. The mould adopts forming by a flexible mould, has a simple structure and high production efficiency, and reduces the cost of the metal bipolar plate; a stamping piece formed by the flexible mould has no phenomena of warping and rebounding; and parts have high quality.