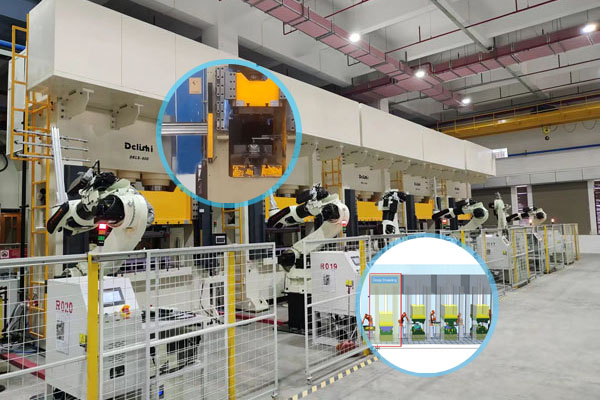
Followings are the key reasons why customization is necessary.
1. Unique Application Requirements
Some industries (e.g., aerospace, automotive, or defense) require presses with special force capacities, stroke lengths, or bed sizes that standard machines don’t offer.
Custom presses can be designed for unusual workpiece shapes or materials (e.g., composites, ceramics).
2. Precision & Control Needs
Advanced industries (like semiconductor or medical device manufacturing) may need ultra-precise pressure control, speed regulation, or automation integration (PLC, IoT, or AI-based monitoring).
3. Space & Layout Constraints
Factories with limited space may require compact, vertical, or horizontal hydraulic presses tailored to fit their production line.
4. Special Safety & Compliance Standards
Industries like nuclear, chemical, or food processing may need explosion-proof, corrosion-resistant, or hygienic (FDA-compliant) presses.
5. High-Volume or Specialized Production
Custom presses can include automated feeding, robotic integration, or multi-stage pressing for mass production efficiency.
6. Energy Efficiency & Sustainability
Custom designs can incorporate energy-saving pumps, regenerative circuits, or hybrid (electric-hydraulic) systems to reduce power consumption.
7. Durability & Heavy-Duty Use
For extreme conditions (e.g., forging, military applications), presses may need reinforced frames, hardened platens, or high-temperature resistance.
Our customized hydraulic press eliminates these inefficiencies by optimizing production processes, reducing labor costs, and minimizing material waste.