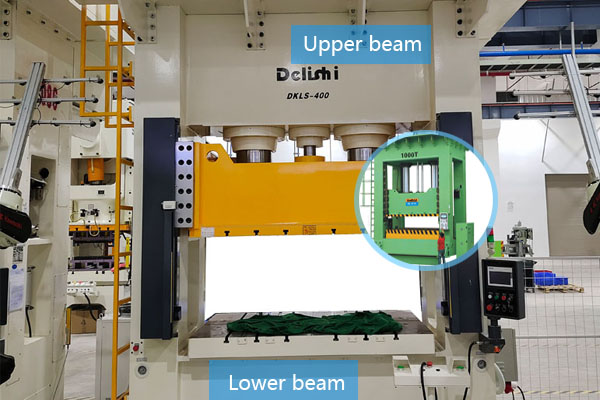
Based on this, we proposed a new double-beam hydraulic press structure. The specific work is as follows:
1. In order to solve the problem of uneven thickness of parts, the traditional slider pressing method is changed to the upper and lower mold clamping method of the workbench. The workbench is installed on the upper and lower beams respectively. During pressing, the upper stroke large main cylinder is used to pressurize the middle of the thin plate steel workbench according to the deflection line of the part under pressure, and the four corners are leveled to ensure that the parts have the same degree of deflection and bending when pressing. The problem of uneven thickness of parts caused by the inconsistency between the slider and the workbench deflection line is effectively avoided, thereby optimizing the large-mass slider.
2. In order to solve the problem of excessive travel of the three-beam slider due to different mold heights, an openable locking mechanism is introduced, so that the upper beam structure can be adjusted along the column, so that the hydraulic press can be adaptively adjusted according to different mold heights, avoiding unnecessary long travel during pressing.
The development of a new double-beam hydraulic press involves several critical steps, including structural design and topology optimization.