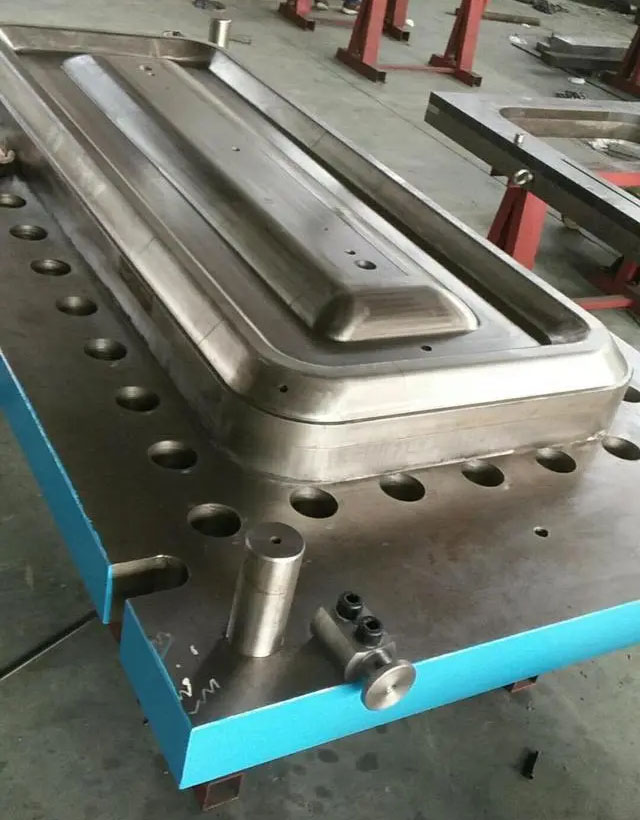
The working table of the hydraulic press for correcting and shaping the train door panel is large. The working table refers to the distance between the slider of the four-column hydraulic press and the working table. The determination of the worktable is mainly based on the size of the pressed workpiece or the size of the mold. Since the train door is a relatively large workpiece, a large hydraulic press for the worktable is selected for production and processing.
Technical advantages of hydraulic press for correcting and shaping train door panel :
1. The structure of the four-column hydraulic press is simple, economical and practical; the I-frame structure has good structural steel properties, high precision, and strong load resistance.
2. The hydraulic control of the four-column hydraulic press adopts an integral cartridge valve system, which reduces leakage points, reliable action and long service life.
3. The electrical system controlled by PLC is compact, sensitive, reliable and flexible.
4. The working pressure and stroke can be adjusted within the specified range according to the process requirements, and the operation is simple.
5. Correction and shaping train door hydraulic press has three operating modes: adjustment, two-hand unit cycle, continuous work (with feeding device).
6. Through the selection of the operation panel, not only two molding processes of fixed stroke and constant pressure can be realized, but also three process operation cycles of cushioning, no cushioning and ejection can be realized.