
☆ Widely used in the following industries
Automotive industry: engines, transmission components press fit (input shaft, output shaft, differential, cylinder head, cylinder liner, oil seal, etc.), steering gear components press fit (gear, pin shaft, etc.), transmission shaft components press fit, gearbox components press fit, brake disc component press fit, etc.
Motor industry: Micro motor component pressing (spindle, housing, etc.), motor component pressing (bearings, spindle, etc.).
Electronics industry: PCB component pressing (plug-in, etc.) Electronic component press fit.
Home appliance industry: home appliance parts pressing, home appliance parts riveting, etc.
Mechanical industry: mechanical component pressing, automated assembly line, vulnerable component life testing, etc.
Other industries: Other situations that require precise control of pressing displacement and pressing force.
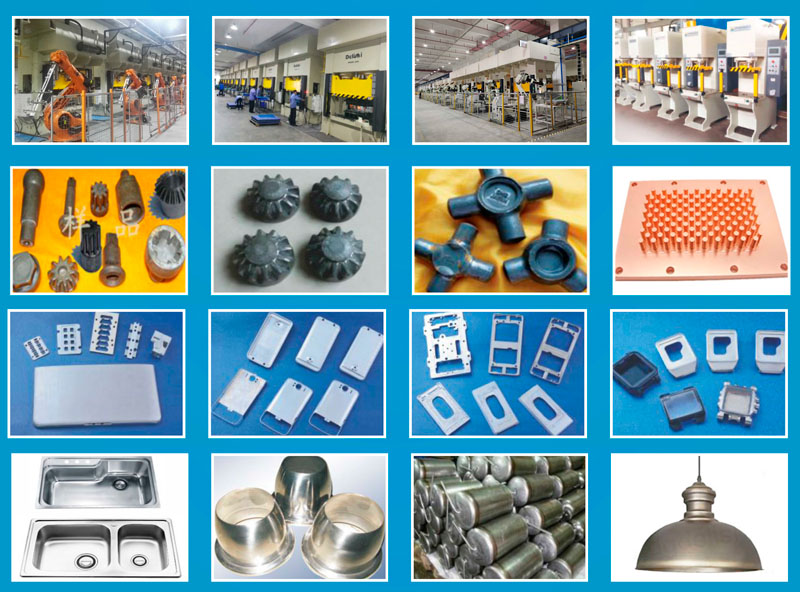
☆ Application of Servo Hydraulic Press Machine
The servo hydraulic press machine are suitable for various stamping processes such as stretching, bending, forming, punching and flanging, and is particularly suitable for the following fields:
1. Automotive components: body covering parts, brake pads, mailbox, chassis, axle housing, bumper;
2. Household appliances: washing machine parts, rice cooker parts, TV parts, refrigerator parts, etc;
3. Kitchen utensils: sink, kettle, stainless steel utensils, and various other containers.
☆ Characteristics of Servo Hydraulic Press Machine
1. Efficient and energy-saving, with electricity consumption saving of 30% -50% compared to ordinary motors
2. Low noise, noise can be controlled at around 60 decibels.
3. The working position, speed, and pressure can be infinitely adjusted.
4. Quick response, high precision in pressure and position repetition.
5. High efficiency, multiple internal protections, and extremely low failure rate.
6. 12 hours of continuous operation do not require cooling oil temperature.
7. The pipeline and joints adopt SEA international standards to prevent pipeline oil leakage.
8. Adopting centralized button control, two control modes (fixed range/pressure), and two operation modes (adjustment/automatic).
10. The machine can be equipped with mold lifting guide rails, external mold insertion guide rails, and automatic mold clamping function.
11. The servo proportional valve controls the edge pressing force, counter edge pressing force, and feeding pressure in segments.
12. The low-voltage intelligent mold closing system has an automatic feedback function for detecting foreign objects, protecting the safety of the mold.
13. Servo motor combined with high-precision oil pump drives segmented control of pressure, speed, and exhaust.
14. Precision control of displacement, speed, and pressure, adjustable on an industrial touch screen.
15. Provide remote network services, machine automatic alarm prompts for faults and maintenance.